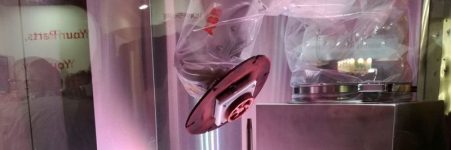
3D Printing – the End of Aluminium Casting?
A new technology makes 3D metal printing possible for mass production.The new “Supersonic 3D Deposition” technology is able to print metal parts in a fraction of the time and can use aluminium and copper powder.
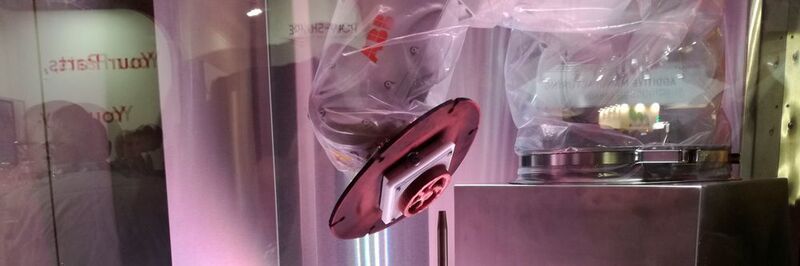
The name says it all: Not only does the company’s name refer to the high speed that is one of the main characteristics of the technology. It also derives from the new technology. “Supersonic 3D Deposition” – or short “SP3D” – is a 3D printing method that is different from all other metal printing technologies like SLM (Selective Laser Melting). Especially the constraints concerning time and cost present an obstacle to adapting these technologies. From the beginning, the focus of “SPEE3D” was to eliminate these obstacles. According to the company, its 3D printer, capable of processing aluminium and copper powder, is able to print metal parts in a fraction of the time and cost of other 3D printers. To achieve this goal, the company has developed a new 3D printing process.
The following viedo by “SPEE3D“ not only portrays the speed of the 3D printing method, it also offers an insight to the process itself:
Here is how Supersonic 3D Deposition works: Air that is accelerated to a speed of u tp three times the speed of sound is shot through a nozzle. Injected metal powders are thereby deposited on a substrate. The high speed or kinetic energy is used to stick the metal particles together. The process forms high density parts with normal metallurgical properties, “SPEE3D” says.
Simple and Flexible Manufacturing on Demand
At Formnext 2017 in Frankfurt, “SPEE3D” presented its printer for the first time to a European public. The official global launch of the company was only announced a week before the trade show started. “SPEE3D was started after I experienced the slow pace and lack of rigor in the high cost, traditional metal 3D printing industry,” said Byron Kennedy, Chief Executive Officer and Co-Founder of “SPEE3D“. “In the past, users had to wait hours or even days to have a standard part delivered to them. Now, “SPEE3D” can print these same parts in mere minutes, on-site and in real time. This enables the accessibility of just in time production – allowing manufacturers the choice and flexibility of printing 10,000 parts or just a single part with ease.”
he process used by the printer called “Light-SPEE3D” also has its draw-backs: The process is far less accurate than other 3D printing technologies, let alone cutting technologies. But the printer is not meant for high-precision parts. At the moment, SP3D is a technology that can replace, for example, aluminium casting, especially if the finished part does not have to follow rigid form constraints. According to the company, applying the 3D printing technology in these cases, users can save money because of time and material savings.
The speed and cost efficiency of the “Light-SPEE3D” printer allows users to produce parts flexibly and easily, from brackets and manifolds to engine components in single or high-volume production quantities, economically, on-demand and at speeds that are 100 to 1,000 times faster than traditional metal 3D print technologies, “SPEE3D” says.